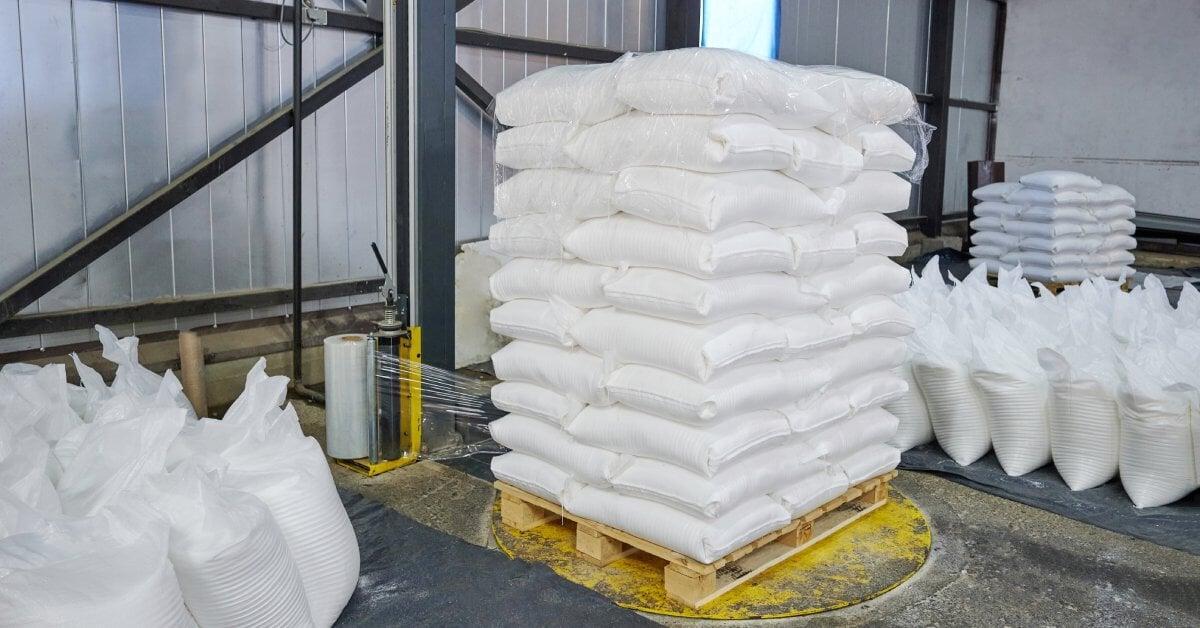
An automatic stretch wrap machine transforms how businesses handle their shipments, including increasing worker safety and cutting costs. These machines not only save time but also provide consistent, high-quality wrapping that manual methods can’t match. From boosting productivity to protecting your bottom line, learn about the reasons why your warehouse needs an automatic stretch wrap machine.
Increases Productivity
Manual wrapping is a slow process that consumes valuable time. Workers spend ample effort bending down, rotating pallets, and working through multiple layers of film. Replacing this process with an automatic stretch wrap machine will result in wrapping pallets faster and redirecting the team’s attention to other important tasks.
With decreased wrapping times, the warehouse can handle greater volumes of goods without delays. Faster throughput improves turnaround times, which is crucial for timely deliveries and maintaining customer trust.
Quality stretch wrapping also saves time during various operations. A properly wrapped pallet makes it simple and fast to move goods safely without worrying about them shifting or falling. This cuts down on the time spent fixing issues caused by damaged or poorly wrapped loads. It also helps organize storage and staging more efficiently.
Consistent Wrap Quality
Manual wrapping errors like uneven tension or inadequate coverage can lead to inconsistent results. If the tension is too loose or the film doesn’t fully cover the pallet, the load becomes unstable and prone to shifting or falling during transport. On the other hand, too much tension might damage the good. Both of these issues can lead to delays, additional expenses, and wasted materials.
Industrial stretch wrap machines eliminate these disparities by providing the same high-quality wrap for every application. Whether it’s a lightweight product or a heavy load, your team can count on precise and secure packaging.
Here’s how stretch wrap machines wrap every pallet securely:
- They use preprogrammed settings to deliver uniform wrapping coverage for every pallet.
- Sensors and adjustable controls adapt the wrap to the specific dimensions and weight of each load, ensuring a snug and reliable fit.
- These machines maintain an even wrapping pattern by rotating the pallet smoothly to prevent weak spots or uneven edges.
Employs the Right Amount of Film
Manual pallet wrapping commonly results in uneven film use. Workers may overcompensate by adding extra layers of wrapping. The manual process lacks the precision of automatic systems, preventing high costs due to consuming more film than necessary.
Automatic stretch wrap machines solve this by stretching the film before applying it, making the film stronger. Employees use rollers to pull and stretch the film without tearing it. Pre-stretching reduces the amount of film needed, saves costs, and ensures tight, secure wrapping to keep loads stable.
Enhances Load Stability
One of the best reasons to get an automatic stretch wrapper for your warehouse is to increase load stability. Whether it’s wrapping pallets, furniture, or oddly shaped products, stretch wrap machines protect goods from damage. The type of stretch wrap machine you choose should match the specific needs of the products your facility handles.
Stretch Wrap Turntables
Stretch wrap turntables are machines with a rotating platform. They spin around the pallet to apply the film. Stretch wrap turntables work best with stable, palletized loads that are uniform in shape and weight. Furthermore, they’re ideal for facilities that handle standard-sized shipments and need a reliable, consistent wrapping solution.
Robot Wrappers
Robot wrappers are mobile machines that move around the load to apply the stretch wrap. They are perfect for wrapping oversized, heavy, or irregularly shaped loads that might not fit on a turntable. This flexibility makes them a great option for facilities dealing with a variety of load types or layouts with limited space.
Rotary Arm Machines
Rotary arm machines keep the load stationary while a rotating arm applies the stretch film. They are an excellent choice for light or fragile loads that could topple over if spun on a turntable. Facilities managing delicate products or high-speed wrapping operations often benefit most from these machines.
Orbital Stretch Wrap Machines
Orbital stretch wrap machines wrap long or oddly shaped items such as pipes, furniture, and lumber. These machines use a horizontal wrapping process where the product passes through a rotating ring that applies the stretch film. They are well-suited for facilities that handle bulky or non-palletized goods requiring secure containment.
Improves Workplace Safety
Manual pallet wrapping requires repeated bending, reaching, and rotating, which can cause strain injuries that lead to long-term pain and diminished workplace productivity. Automating stretch wrapping prevents these workplace injuries while making the process more efficient.
Additionally, stretch wrap machines include safety features to make them easy and safe to operate. Most models come with emergency stop buttons, sensors, and control settings to prevent accidents during use. Their stable design and hands-off operation greatly reduce the chance of injury compared to manual wrapping, making them a safe choice for busy warehouses.
Minimizes Product Damage
A poorly wrapped pallet is a disaster waiting to happen. Damaged goods due to inadequate packaging can cause decreased sales and reputational harm. Automatic stretch wrap machines provide a tight, protective wrap that withstands transit-related stresses.
The products will remain shielded from environmental exposure, shifting, and impact. By reducing product damage rates, this automation enhances customer trust and prevents financial losses stemming from careless handling.
Adapts to High-Demand Periods
High-demand periods—such as holidays, peak shipping seasons, and sudden increases in orders—create significant challenges for manual wrapping. The pressure to wrap more pallets quickly can overwhelm workers, leading to slower output, inconsistent wrapping, and exhaustion or injuries. This can create bottlenecks in productivity and make it difficult to meet customer expectations.
Automatic stretch wrappers provide a clear solution to these limitations by ensuring fast, consistent wrapping without draining workers’ energy. These machines handle large volumes with ease, improving efficiency while maintaining high wrapping standards that protect the loads. By automating this process, businesses can keep up with demand, reduce workplace strain, and maintain smooth operations during busy periods.
Investing in an automatic stretch wrap machine streamlines your operations by boosting efficiency, enhancing safety, and reducing waste. Industrial wrapping machines ensure secure, consistent wrapping that protects products during transit, cutting down on damage and costs. The automated process not only prevents workplace injuries but also keeps pace with high-demand periods effortlessly. By adopting this technology, businesses can enhance productivity, lower risks, maintain reliability, and stay resilient regardless of market fluctuations.