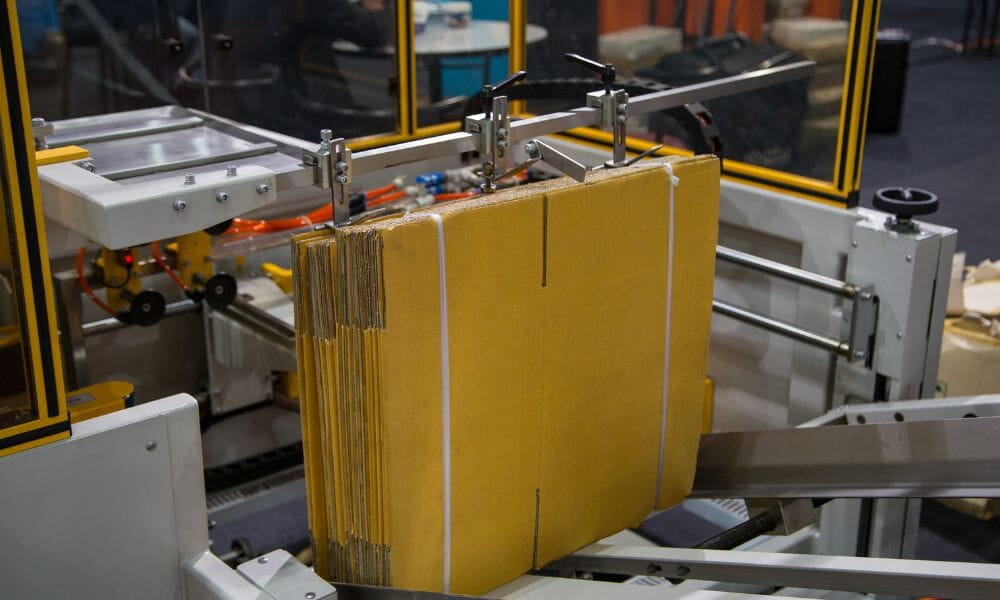
When it comes to case forming, incorrect settings, worn-out components, and unsuitable materials can cause skewed corners, jams, and inadequate seals. Troubleshooting these common case forming issues will reduce downtime and improve overall efficiency. Use these tips to quickly identify and fix case forming problems.
Skewed Corners
Skewed corners refer to the improper alignment or joining of the edges at the corners of a box, resulting in a case that’s not perfectly square. This misalignment can compromise the structural integrity of the case, making it less effective at protecting its contents during shipping and storage.
To address skewed corners in case forming, it’s essential to first check the cardboard material tolerances, ensuring they fall within the specified range for your machinery. Variations in thickness, stiffness, or moisture content of the cardboard can lead to improper folding and sealing, resulting in skewed corners.
After verifying material tolerances, ensure the machine’s guides and folding plates are aligned according to the manufacturer’s specifications. Check for wear and tear on these components and replace them when necessary.
Jammed Case Erectors
A jammed case erector can bring your packaging line to a standstill. This often happens when there’s a backlog of materials, causing cases to become stuck.
The following factors can cause case erectors to jam:
- Inconsistent material quality: This includes variations in cardboard thickness, stiffness, or moisture content.
- Incorrect machine setup: Improper alignment or calibration of the machine’s components can lead to jams.
- Worn-out parts: Overuse leads to wear and tear of mechanical parts, affecting operation.
- Improper case size adjustments: Incorrect adjustments for different case sizes can lead to jams.
- Adhesive issues: Inadequate or excessive glue application causes cases to stick together or to the machine.
- Foreign objects: Small items or debris can get caught in the machinery, obstructing the case path.
To troubleshoot this common case forming issue, start by safely powering down the equipment and carefully removing any visible obstructions or jammed cases. Next, inspect the machine for signs of wear and tear on moving parts and replace damaged components.
Check the machine setup and adjustments to ensure they are correct for the size and type of cases being processed. Modify alignment, pressure settings, or adhesive application as needed. Lastly, review the case material and ensure it meets the specifications for thickness, moisture content, and rigidity to prevent future jams.
Inadequate Sealing
Poorly sealed cases risk opening during transit, compromising the safety of the products within. First, inspect the sealing equipment and replace any worn tape heads or sealing materials that aren’t adhering as they should.
You may need to adjust the pressure and placement of the sealing mechanism. Inadequate pressure will result in a weak seal, while incorrect placement can cause uneven or partial seals. Regular checks and calibrations of the sealing machine are necessary to maintain the integrity of all case seals.
Regular maintenance, precise calibration, and careful material selection are fundamental to resolving case forming problems. By implementing systematic checks and replacing worn components, businesses can protect their products and present them in the best way.
If you’re adding new equipment to your packaging line, remember that quality case erectors reduce the incidence of jams, skewed corners, and inadequate sealing. Invest in a well-constructed, high-performing case former for minimal downtime and simple maintenance.