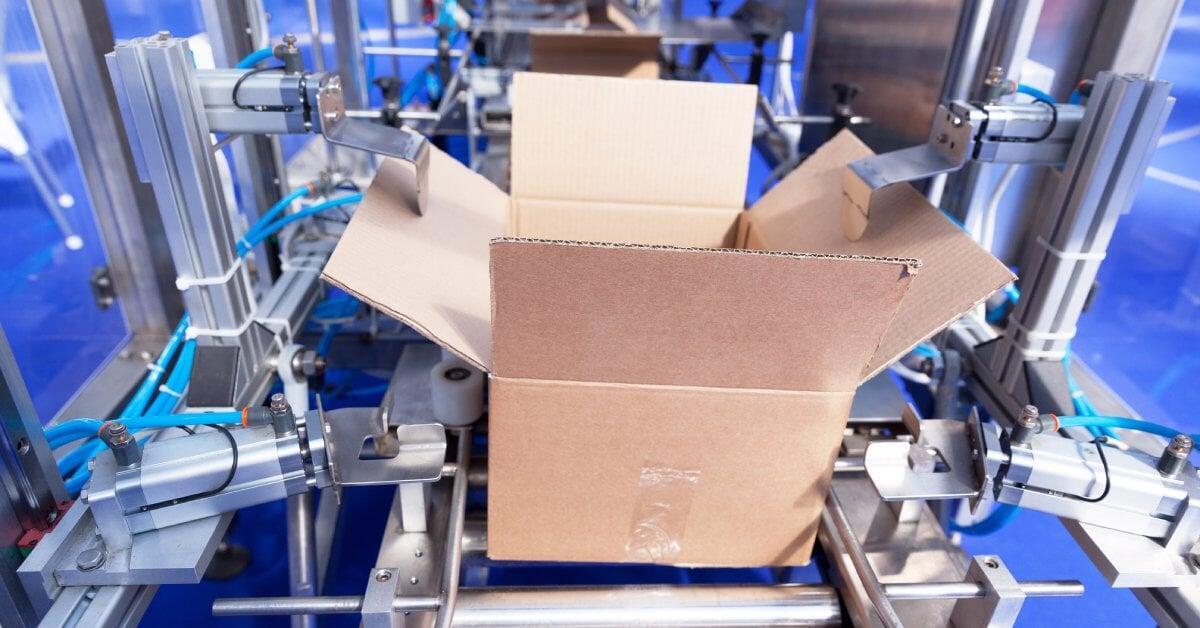
You can edit text on A case erector automates one of the most time-consuming manual tasks in packaging. It takes flattened corrugated boxes and folds them into perfectly formed cases, which improves efficiency, reduces labor costs, and promotes consistency in case quality. Whether you're running a small operation or managing a high-volume packaging line, selecting the right case erector is critical to optimizing performance. From compatibility with case sizes to automation levels, here are the things to consider when choosing a case erector.
Machine Speed
The speed of a case erector, also called a box erector or case former, is a crucial factor in ensuring your production line operates efficiently. Machines are typically rated by their cases-per-minute (CPM) output. For high-volume production lines, a machine with a higher CPM is vital to keeping up with demand and avoiding bottlenecks. However, opting for a machine that’s unnecessarily fast for your needs might result in overspending.
On the flip side, slower machines can hold back production and cost you valuable time. When determining the ideal speed for your case erector, consider your current production requirements and potential future growth. Investing in a machine that slightly exceeds your current production demands will prepare your business to scale without needing immediate upgrades.
Ease of Maintenance
Equipment downtime can be a costly disruption, so it’s important to select a case erector that’s user-friendly and easy to maintain. Machines with accessible components and straightforward maintenance instructions simplify upkeep and reduce downtime. Features such as tool-free maintenance access can make a big difference in minimizing the effort and time needed for repairs.
Additionally, models with clear diagnostic systems provide detailed error messages or visual indicators that help you pinpoint specific issues within the machine. This information reduces troubleshooting time and helps operators resolve issues more quickly.
Reliability and Durability
Long-term reliability is key when investing in packaging equipment. A case erector must consistently produce high-quality cases even under the stress of high production volumes. Machines built with durable materials and precision-engineered parts are less likely to break down or require frequent replacements.
Researching the track record of a specific model or manufacturer can provide valuable insights into its reliability. Look for reviews, case studies, or customer testimonials to ensure the case erector you’re considering can withstand regular use over time.
Compatibility With Case Sizes
Packaging lines often handle a variety of case sizes, making compatibility an essential consideration. Some box erectors are designed to handle a single case size, while others can easily adjust to accommodate a wide range of box dimensions. If your business requires frequent changes in packaging sizes, opting for a flexible machine will save you from needing multiple units.
Keep in mind that a machine with multi-size compatibility may have slightly higher upfront costs, but the versatility will pay off in the long term if it’s what your business needs. An adaptive case former will reduce downtime during size changes and meet evolving packaging needs caused by a shift in product offerings, market demands, or consumer preferences.
Space Requirements
Another critical factor to evaluate is the case erector’s physical footprint. If your production floor is already crowded, make sure the machine fits comfortably in the space without disrupting other operations or workflow. Compact models can be an excellent choice for businesses with limited floor space.
However, don’t just consider the static footprint. Many case erectors also require extra room for case feeding and discharge, as well as space for operator access during troubleshooting or maintenance. Always measure your available space and consult the manufacturer’s specifications before making a purchase.
Safety Features
Automation often enhances safety by minimizing direct human interaction with machinery. Case formers often have robust safety features such as emergency stops, safety guarding, and sensors that detect blockages or other anomalies. These features reduce the risk of accidents, especially in fast-paced production environments.
A machine that meets or exceeds safety standards not only protects your workers but also ensures compliance with industry regulations. This can save you from potential fines or legal issues in the future.
Cost and ROI
When choosing a case erector, consider its total cost of ownership rather than just the initial purchase price. Operating expenses, energy efficiency, maintenance requirements, and long-term usability all influence the total cost of ownership. A machine with a slightly higher upfront cost but lower operating expenses might be more cost-effective over time.
Additionally, calculate how quickly the machine will generate a return on your investment. Reliable equipment with improved efficiency can reduce labor costs and enhance production speed, ultimately improving your bottom line.
Level of Automation
The level of automation you require from your box erector machine depends on the scale of your operation. Fully automated case erectors require minimal manual intervention, reducing labor costs and improving efficiency. However, they tend to come with higher upfront costs.
For smaller operations with less demanding production volumes, semi-automated case erectors may be more cost-effective. These machines still streamline the packaging process but rely on some manual assistance, offering a balance between investment cost and automation level.
Ease of Integration
A case erector is just one component in a larger packaging line, and seamless integration is critical to minimizing bottlenecks and creating smoother workflows. Ensure that the machine you choose can connect with your existing upstream and downstream equipment, such as fillers or carton sealers. Consider whether the case erector has adjustable settings or open communication protocols like Ethernet/IP. These features make it easier to integrate the machine into diverse production environments and adapt to future equipment upgrades.
Below are the key steps to integrating a new case erector into your packaging line:
- Assess the packaging line’s operational speed and the dimensions and types of cases it processes to ensure compatibility with the new case erector.
- Determine where to place the case erector to maximize workflow efficiency while maintaining access for operation and maintenance.
- Verify that your production facility has the appropriate power supply and communication interfaces, such as Ethernet/IP, to support the case erector.
- Provide operators and technicians with proper training on how to use and maintain the new equipment to reduce errors and downtime during transition.
- Run the case erector with test materials to confirm that it operates correctly and integrates seamlessly with the upstream and downstream machines.
- After installation, monitor performance over time and make any necessary adjustments to ensure productivity and reliability.
A case former is a key investment that can transform packaging efficiency and keep your packaging line agile. By evaluating the machine’s speed, compatibility with case sizes, ease of maintenance, safety features, and reliability, you can ensure smooth and efficient workflows. Additionally, balancing cost and space constraints with the level of automation required will help meet current needs while preparing for growth. A well-integrated and properly selected case erector not only improves productivity but also delivers long-term cost savings and operational consistency.