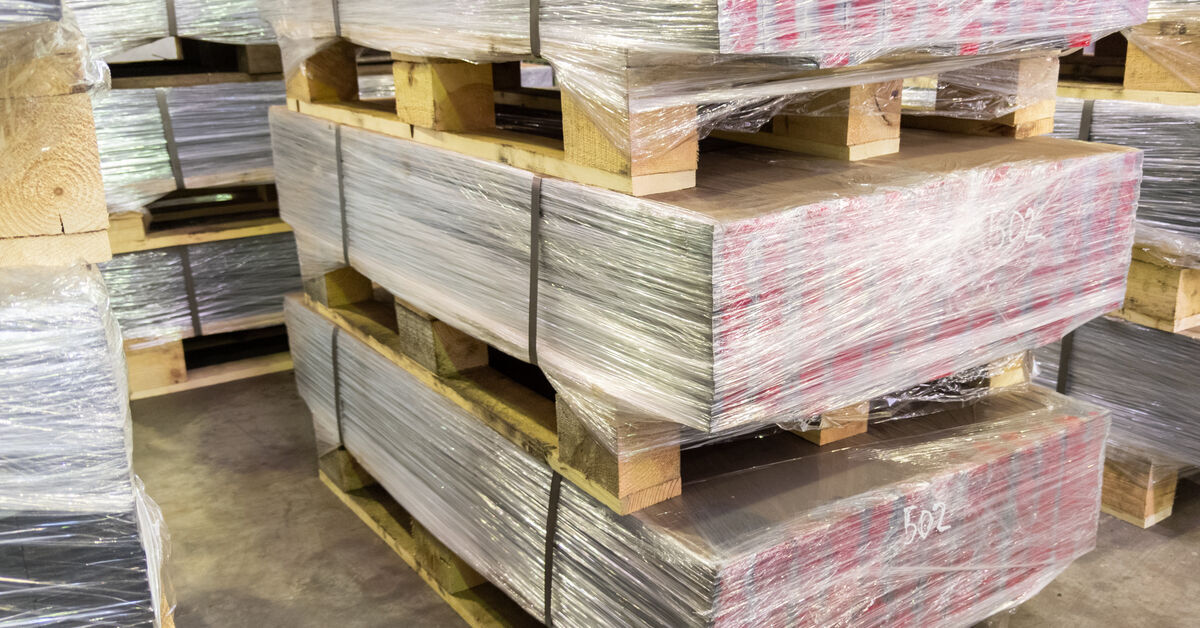
Shrink wrap and stretch wrap are two of the most commonly used materials in packaging. While they may seem similar, they serve unique purposes and differ in terms of application, material behavior, and overall effectiveness. Choosing the right option depends on your specific needs, whether it’s protecting items, securing shipments, or maintaining product presentation. Explore the key differences between shrink wrap and stretch wrapping to understand their applications.
Purpose
Shrink wrap is best for protecting products from dust, moisture, and tampering. It’s particularly popular in retail settings for boosting cleanliness and presentation. Shrink wrap conforms tightly to items to ensure they stay intact and well-protected from external elements.
Stretch wrapping, on the other hand, excels at bundling and stabilizing products for transit. It is commonly used to secure items on pallets to make sure shipments remain steady throughout transportation. Its cling properties make it ideal for logistics and warehousing operations where stability is a priority.
Material Behavior
Shrink wrap is a thin plastic material that shrinks tightly around an item when heat is applied. The heat causes the wrap to contract and conform snugly to the product’s shape, creating a secure and protective barrier. This tight seal not only keeps out dust and moisture but also helps prevent tampering, making it highly effective for packaging.
Stretch wrapping clings tightly as it is wrapped around items without the use of heat. Packaging equipment automates wrapping pallets with stretch wrap, which speeds the processing time and provides consistent application. Stretch wrappers minimize wasted material by pre-stretching the stretch wrap, allowing it to cover more surface area with less plastic. Pre-stretching enhances the material’s elasticity and cling, ensuring a tighter, more efficient hold on packaged items.
Common Industries
The food packaging industry widely uses shrink wrap to keep products fresh and protected from contamination. Retail businesses rely on it to create tamper-evident seals for items like electronics or cosmetics, making sure customers receive unopened and secure products. Manufacturing companies often use shrink wrap to bundle items together, making them easier to handle and transport. Its versatility and ability to provide a clear, durable barrier make this material a valuable tool across these industries.
Stretch wrap is widely used in logistics to secure pallets and keep shipments stable during transport, reducing the risk of damage. The agriculture industry relies on it to bundle hay bales and shield crops from dirt and moisture, helping maintain quality. In construction, stretch wrap protects building materials like lumber, pipes, and bricks from weather exposure, ensuring they stay in good condition. Its ability to tightly hold and shield items makes stretch wrap a key tool across many industries.
Cost
Shrink wrap tends to involve higher costs. This is primarily due to the need for specialized heat-based equipment and the energy required during the wrapping process. It is best suited for applications where presentation and protection justify the higher expense.
The cost of stretch wrap is influenced by factors like the material type and thickness, with higher-quality or thicker wraps typically costing more but offering increased durability. The size and weight of the load also play a role, as larger or heavier items may require more wrap or stronger materials. Additionally, the type of equipment used for application, whether manual or automated, impacts expenses, as automated machines can reduce labor costs but require a higher upfront investment. Together, these factors affect not only the price of the wrap itself but also the efficiency and cost-effectiveness of the wrapping process.
Application Process
Shrink wrap and stretch wrapping also require different application methods and tools. Shrink wrap is placed loosely around the item, ensuring complete coverage before sealing any open edges. Using a heat gun or a shrink tunnel, heat is applied evenly to shrink the material tightly around the product, creating a secure and snug fit. It’s important to distribute heat consistently to avoid wrinkles or weak spots in the wrapping.
Stretch wrap application begins by selecting the appropriate type and size of wrap to match the load requirements. The wrap is secured to the base of the load, either manually or with a stretch wrapping machine. It is then wrapped around the product in overlapping layers, providing full coverage and stability. Maintaining consistent tension throughout the process is crucial to keep the load secure while avoiding overstretching the wrap.
Comparing Stretch Wrap Patterns
Stretch wrapping patterns include options like spiral wrapping, full coverage, and banding, each tailored to specific load requirements. Spiral wrapping involves wrapping in a continuous upward or downward motion, which is ideal for tall or irregularly shaped loads. Full coverage provides complete wrapping of the load, offering maximum stability and protection—this method is often used for fragile or highly stacked items. Banding focuses on securing key areas like the top, middle, or bottom of the load, which is suitable for smaller or more compact items that need less overall coverage but firm containment.
Strength and Thickness
Shrink Wrap Weaknesses and Care Tips
Shrink wrap is thinner by design. While effective for protection and presentation, it’s vulnerable to certain factors. It can be easily punctured or torn by sharp edges, rough handling, or contact with abrasive surfaces, which compromises its protective seal. Additionally, shrink wrap is sensitive to extreme temperatures—prolonged exposure to heat can cause it to warp or melt, while freezing conditions may make it brittle and prone to cracking.
To minimize these risks, avoid unnecessary friction or stress on the wrap. Store shrink-wrapped products away from heat, cold, and sunlight to preserve their durability and protection.
Stretch Wrap Vulnerabilities and Usage Tips
Stretch wrap, while durable, is vulnerable to damage from sharp objects, which can puncture or tear the material, compromising its effectiveness. Overstretching during application can also weaken the wrap, reducing its ability to hold loads securely. Environmental factors like prolonged exposure to extreme heat or sunlight may cause the wrap to degrade or lose elasticity.
Using stretch wrappers with adjustable tension settings ensures the film is applied without overstretching. Operators should monitor the wrapping process carefully to confirm the tension is consistent and suitable for the load. Once wrapped, goods should be stored in cool, dry areas away from direct sunlight or extreme heat to prevent material degradation.
While both shrink wrap and stretch wrap serve vital roles in packaging, they are tailored for different purposes. Shrink wrap safeguards products and enhances their presentation, while stretch wrap is best suited for securing shipments in transit. Their material behaviors and application methods differ, with shrink wrap relying on heat and stretch wrap leveraging elasticity for secure bundling. By weighing your goals, budget, and desired outcomes, you can determine the best type of material and packaging equipment for your business.bsite. Alternatively, when you select a text box a settings menu will appear. your website by double clicking on a text box on your website. Alternatively, when you select a text box.