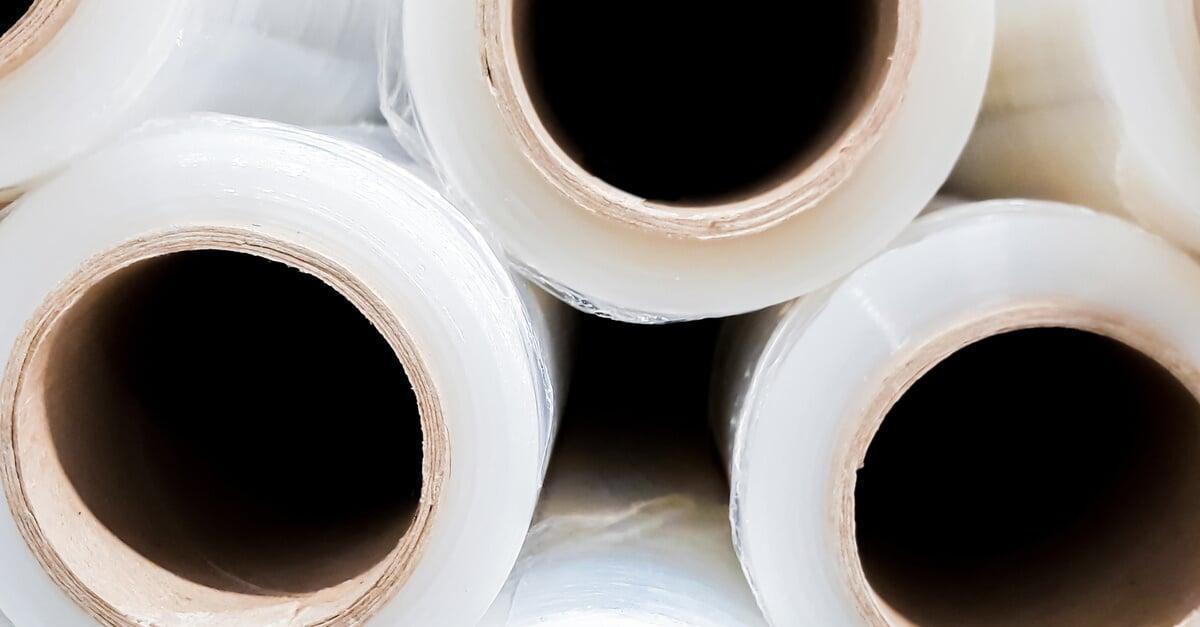
Using the wrong film can lead to inefficiencies in your warehouse, unnecessary costs, and even damaged products. Selecting the right film for your stretch wrapping machine is vital for ensuring the safety and security of your loads during storage and transport. This guide will help you evaluate the most relevant aspects—from load requirements to wrap characteristics—so you can find reliable materials for your equipment and goods.
Film Type
The type of stretch film you use—blown or cast—affects the wrapping process and final results. Machines optimized for cast film may not achieve optimal performance with blown film and vice versa. Consult your machine's user manual or manufacturer to clarify the compatibility.
Cast Films
Cast films are made using a process that delivers a smooth, clear finish, making it easy to inspect wrapped loads. These films offer excellent stretchability and consistency, which improves the efficiency of wrapping machines. They’re quiet to unwind and are often used in applications where speed and visibility are important. Common applications include retail packaging, securing food products, and high-speed wrapping operations in warehouses and distribution centers.
Blown Films
Blown films are produced through a process that creates a tougher, more durable material resistant to tears and punctures. They have a tackier surface, offering a superior cling for securing loads, especially irregular or heavy ones. Blown films are ideal for applications that demand high durability, even in challenging conditions. They are often used to wrap construction materials, secure heavy-duty shipping loads, and protect items stored outdoors.
Stretch Capacity
The stretch capacity of your film must align with your machine’s pre-stretch capabilities. High pre-stretch machines require you to use films with excellent elasticity to ensure consistent performance. This compatibility minimizes irregularities and prevents material breakage during operation.
Choosing a film with the right stretchability not only improves load stability but also optimizes material usage. Proper stretch settings and film elasticity lead to reduced waste and greater operational efficiency over time.
Film Thickness and Load Weight
Stretch film thickness refers to how thick or thin the film is, typically measured in microns. It’s important because the right thickness ensures your load is secure, stable, and protected during transport without using more material than necessary.
Gauge refers to the thickness of a stretch wrap, with higher gauges offering greater resistance to tearing or breaking. A 50-gauge wrap has a thickness of 0.0140 mm, whereas a 100-gauge wrap is 0.0254 mm thick. You can refer to a conversion chart to see what a film gauge equals in millimeters, microns, or other standard measurement values.
To ensure the stretch film thickness is right for your machine, you can check the manufacturer’s guidelines or the product specifications for recommendations.
Light Loads
For lighter loads of tissue paper, empty bottles, or other lightweight items, a thin film between 45- and 60-gauge typically works best. This thickness is ideal because it provides sufficient wrap without adding unnecessary weight or cost. It’s also easier to stretch, making it compatible with arm and ring machine wrappers, which are designed for gentle handling of fragile or light materials.
Thin gauge film helps stabilize light loads effectively without causing damage to delicate items. Its stretchability allows for a snug wrap while maintaining visibility, making it easy to identify the contents within.
Medium Loads
Medium loads weighing up to 2,400 pounds can be covered with an 80-gauge film, which is the most common gauge of stretch wrap. This film strikes a balance between flexibility and strength, offering enough durability to secure more substantial items. Turntable machines, arm wrappers, and ring wrappers are all well-suited for handling medium loads.
Using a thicker film ensures better load stability and reduces the risk of tearing or punctures during wrapping or transportation. It’s also cost-effective because it avoids overuse of material while still meeting the demands of medium-weight applications.
Heavy Loads
Heavy loads such as steel drums need a thicker film above 100 gauge for optimal security. This thickness provides the extra strength and resistance required to handle the weight and stress these loads endure during storage and transportation. Turntable wrappers, arm wrappers, and ring wrappers can manage the application of these robust films.
Thicker films ensure heavy loads remain stable by offering superior puncture resistance and durability. They excel in protecting bulky or high-stress loads from shifting or damage. While this film can cost more than others, its resilience minimizes the risk of product loss or accidents, making it a reliable choice for challenging packaging tasks.
Machine Speed
Films incompatible with the speed of the stretch wrap machine can cause performance issues such as breakage or improper wrapping. High-speed, fully automatic stretch wrappers with pre-stretch systems typically require a high-quality, premium stretch film. These films are designed to handle the intense demands of fast operation, providing excellent load stability and minimizing the risk of film breakage.
On the other hand, conventional stretch wrapping equipment operating with minimal stretch can often use an economy-grade stretch film. These films are cost-effective and work well in applications where there’s less demand for intense stretching. For machines with moderate pre-stretch capabilities, a mid-range stretch film is the best fit, balancing durability and performance without exceeding warehouse budgets.
Load Stability Requirements
To select the right stretch wrapping film for your machine, consider the wrapping technique you’ll use. The wrapping technique you need to use on a load depends on factors such as the load’s size, shape, and level of protection. These considerations determine whether techniques such as banding, full coverage, or spiral wrapping will be most effective.
Banding involves wrapping stretch film around small sections of a load to hold it together. Full coverage, on the other hand, means wrapping the entire load to protect it from external elements. Spiral wrapping secures loads by wrapping the film in a spiral pattern. It’s ideal for irregularly shaped, tall, or oversized items.
Here are general guidelines for choosing the right type of stretch wrap for each wrapping technique:
- For banding, a stretch wrap film needs a high level of elasticity to grip tightly around smaller sections without tearing.
- Full coverage requires a stretch wrap film with greater thickness and strength to protect the load completely from dirt, moisture, and potential damage. The film should also have excellent cling to stay in place and ensure the load remains stable during transport.
- When spiral wrapping, the film must combine moderate elasticity with good holding power to effectively secure irregularly shaped or larger loads.
The right stretch film can make all the difference for ensuring your loads are secure and stable during storage or transport. Choosing between cast and blown films, understanding how film thickness supports different loads, and aligning the film’s properties with your machine’s performance are all essential for achieving reliable protection. With careful film selection, you’ll achieve reliable results, support operational efficiency, and protect your stretch wrap machine’s components.