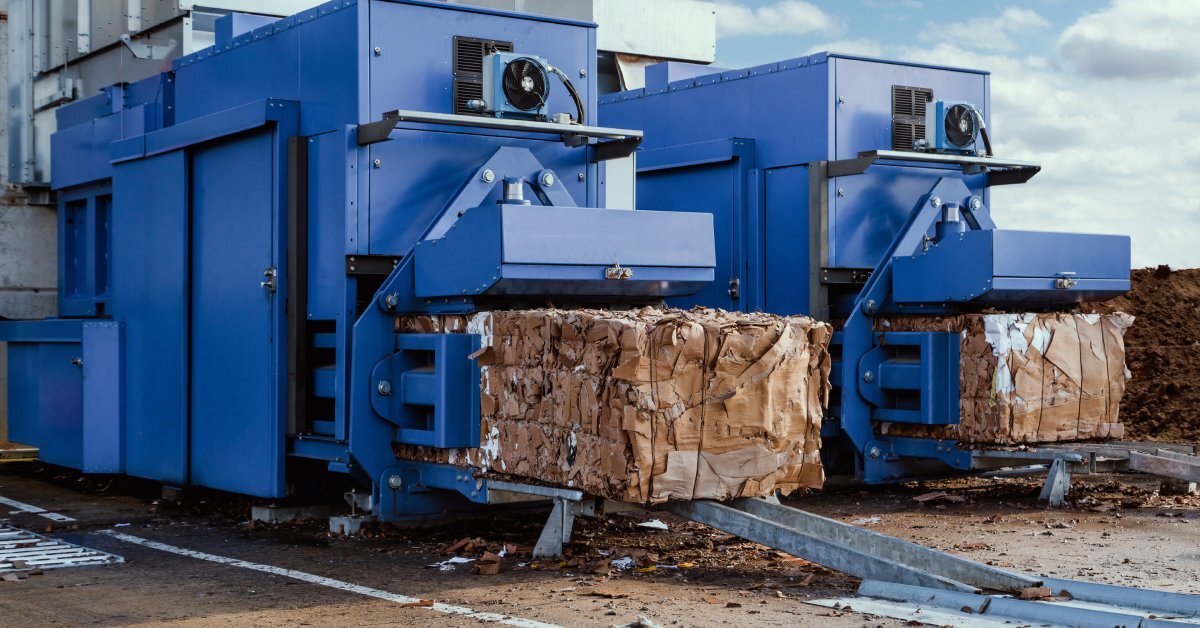
Efficient waste management is a priority for facilities of all sizes. Whether you’re running a large distribution center, a warehouse, or a retail store, handling waste in a streamlined, cost-effective way is critical to maintaining both environmental and operational standards.
Among the powerful tools that can help achieve this is the vertical baler. These machines compact recyclable materials like cardboard, plastic, and more into bales, significantly reducing waste volume while optimizing storage and transport.
However, with numerous models and features available, selecting the best vertical baler for your facility’s needs can feel overwhelming. This guide will walk you through every aspect you need to consider so you can make an informed decision.
The Benefits of Using a Vertical Baler
Vertical balers are highly efficient machines that offer powerful benefits for waste management across a range of industries.
Space Saving
The machines’ ability to reduce waste volume allows facilities to save a significant amount of floor space, which is especially valuable in environments where every square foot matters. By compacting recyclables into manageable bales, vertical balers reduce clutter and create a more organized workspace, contributing to improved safety and efficiency.
Cost Effective
Beyond saving space, vertical balers are a cost-effective solution for handling recyclable materials. Partnering with a recycling company to haul compact bales often results in reduced transportation costs because the compacted waste takes up significantly less room in transport vehicles. Additionally, some businesses turn this efficiency into a revenue stream by selling their recyclable bales to manufacturers who repurpose the materials.
Environmental Impact
Vertical balers are also an important tool for businesses aiming to improve their environmental impact. By compressing recyclable materials like plastic and cardboard, these machines enable businesses to divert waste from landfills, reducing their carbon footprint. This aligns with growing societal and regulatory demands for businesses to adopt sustainable waste management practices. Ultimately, vertical balers strike a balance between operational efficiency and environmental responsibility, making them a valuable asset for modern facilities.
Factors To Consider When Choosing a Vertical Baler
When it comes to selecting the best vertical baler for your facility, several important factors need to be taken into account. From the type of processed materials to space considerations, understanding these elements will ensure that your choice meets your operational needs.
Material Type
The types of materials your facility handles play a significant role in determining the right vertical baler. While many balers process common recyclables like cardboard and plastic, certain models are better suited for specific materials. For example, some manufacturers optimize balers for larger, denser plastics, while others design them for softer materials like textiles. Selecting a baler designed for your facility’s primary material ensures efficient performance and extends the machine’s lifespan.
Bale Size and Weight
The size and weight of the bales a vertical baler produces should align with your facility’s processing and storage needs. Smaller operations might require compact bales that are easy to handle and transport, whereas larger facilities with higher output levels may demand heavier, bulkier bales that optimize haulage efficiency. Matching your baler selection to the right bale size and weight will help streamline transportation and further reduce logistical costs.
Throughput
Every facility has different output requirements, making it important to assess how much recyclable material you process daily. A high-throughput operation that handles significant amounts of waste each day will benefit from an industrial-grade vertical baler capable of keeping up with that demand. On the other hand, smaller-scale operations can opt for more compact models that don’t require industrial-grade capacity. Choosing a baler that can handle your specific workload will prevent bottlenecks and keep productivity on track.
Facility Space
When selecting a vertical baler, it’s necessary to evaluate the available space in your facility. Vertical balers come in different sizes, and their dimensions should fit comfortably within your operational layout. Compact balers are a great choice for facilities with limited space, while larger facilities can accommodate industrial-sized balers. Additionally, consider the machine’s required clearance for loading and unloading materials. Making sure the baler fits within your spatial constraints will save you time and frustration down the line.
Power Requirements
Vertical balers can differ in their power sources, typically categorized as electric or hydraulic. Often considered more energy-efficient and environmentally friendly, electric balers are an excellent choice for facilities prioritizing sustainability. Hydraulic balers, on the other hand, offer high performance and are better suited for heavy-duty operations that require significant force to compress dense materials. Assess your facility’s power infrastructure and overall energy goals to find the right fit.
Safety Features
Safety should always be a primary concern when incorporating machinery into your facility. Vertical balers have various safety features, such as emergency stops, automatic shutoffs, and interlocked doors, to protect operators from potential hazards. Choose a model that complies with safety standards and offers robust features to ensure the safety of your staff during operation. Regular staff training on the use and maintenance of balers should also be a part of your facility’s safety program.
Maintenance Tips for Your Vertical Baler
A well-maintained vertical baler can offer years of trouble-free performance. Start by establishing a regular inspection schedule to identify potential wear and tear on components like belts, motors, and hydraulic systems. Cleaning the baler, especially in areas prone to dust and debris buildup, will prevent operational inefficiencies and prolonged downtime.
Another key aspect of maintenance involves lubricating moving parts to reduce friction for smooth operation. It’s also advisable to monitor the condition of the baler’s hydraulics regularly, as these components are crucial for the baling process. Whenever necessary, consult the baler’s manual or engage with professional technicians for any complex repairs. By sticking to a consistent maintenance routine, you can maximize your baler’s lifespan and safeguard your investment.
Optimize Waste Management With the Right Baler
Selecting the best vertical baler for your facility’s needs is both a practical and strategic decision. The right baler can save space, reduce costs, and align your operations with sustainable waste management practices. By considering factors like material type, throughput, power requirements, and facility space, you can identify a baler that seamlessly integrates into your workflow.
If you need expert advice on finding the perfect baling machine, reach out to our experienced team at PackSmart. We offer a variety of automated and manual machines for facilities with high levels of waste. Investing in the right vertical baler keeps your facility equipped to handle waste efficiently and responsibly, setting you up for long-term operational success. Contact us today to learn more.