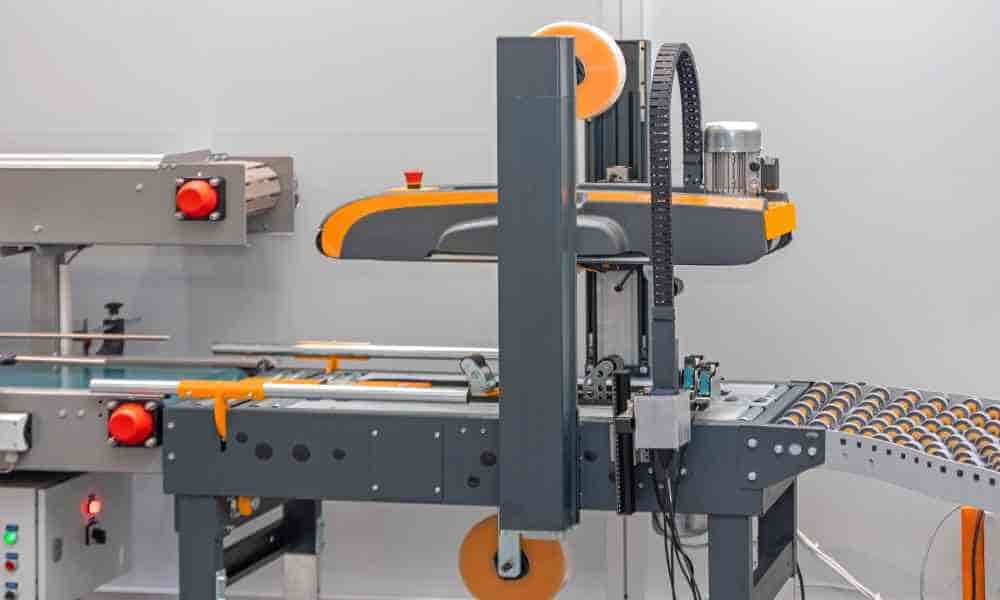
Automatic and semi-automatic case sealers, also called carton sealers, save time by creating reliable seals on cartons and boxes. However, as with any machinery, a poorly maintained case sealer can lead to decreased efficiency, frequent breakdowns, and increased operational costs. All these impact the overall productivity of your packaging line. Follow these essential maintenance tips to extend the life of your case sealer and protect your products.
Regular Cleaning
Dust, debris, and adhesive residue can accumulate over time, leading to clogs, faulty sealing, and reduced efficiency. Accumulated debris can wear out critical components faster, resulting in unexpected downtimes and costly repairs.
To prevent these problems, establish a routine cleaning schedule that involves wiping down the exterior and interior components of the machine, especially the rollers, belts, and adhesive application mechanisms. Using manufacturer-recommended cleaning agents will ensure you don’t damage sensitive components while effectively removing dirt and grime.
Inspect Moving Components
With regular inspections of moving parts, you can identify wear and tear before it leads to machine failure. Belts, chains, and rollers experience constant motion and friction, which makes them particularly susceptible to damage. Schedule periodic inspections to check for signs of wear, cracks, or misalignment in these components.
To optimize your carton sealer’s efficiency and reliability, inspect the following components:
- Belts: Check for cracks, fraying, or stretching that could affect the machine’s efficiency.
- Chains: Inspect for rust, wear, or tension issues that may impede smooth operation.
- Rollers: Look for signs of wear, buildup, or misalignment that can disrupt the sealing process.
- Gears: Ensure there are no broken teeth or excessive wear that could lead to operation failures.
- Bearings: Examine for noise, play, or damage that could cause reduced performance or part failure.
Replace Worn Parts
Replacing worn or damaged components such as blades, rollers, and heating elements helps maintain optimal sealing quality. Over time, these parts can degrade, leading to subpar seals that may compromise the integrity of the packaging. Regular inspections and prompt replacements will ensure that your case sealer continues to perform at its best.
Neglecting to replace worn parts can result in decreased efficiency and increased wear on other components, leading to more extensive and costly repairs. Consider keeping spare parts on hand to minimize downtime during repairs. Additionally, sourcing your packaging equipment from a supplier that carries an extensive parts inventory makes maintenance faster and easier.
Lubricate
Lubrication reduces friction and extends the life of your case sealer's moving components. Follow the manufacturer’s recommendations for lubricating bearings, shafts, and other mechanical parts. Using an incorrect type or amount of lubricant can attract dust and contaminants, which can further impede performance or lead to breakdowns.
Over time, friction can cause parts to degrade and fail, resulting in costly repairs. Regular lubrication helps prevent overheating and excessive wear, ensuring that components move smoothly and efficiently.
When To Lubricate Components
Lubricate components at least once a month or as recommended by the manufacturer. You may also need to lubricate if you notice an increase in operational noise, such as squeaking or grinding sounds, coming from the machine’s moving parts. Furthermore, slower or irregular movement of the machine’s parts may indicate a need for lubricant.
Adjust Belt Tension
Proper belt tension is crucial for your carton sealer's conveyor system. Belts that are too loose can slip, causing irregular movement and inefficient sealing. Conversely, belts that are too tight can experience excessive wear and tear, shortening their lifespan.
Check and adjust the belt tension regularly according to the manufacturer's guidelines. Always power down and unplug the case sealer to safely perform adjustments. Properly tensioned belts will ensure consistent carton movement through the sealer, resulting in uniform sealing.
Check Sealing Temperature
Machine operators should monitor and calibrate the sealing temperature to achieve consistent and effective seals. Excessively high temperatures can cause overheating and damage to the cartons. Conversely, excessively low temperatures create weak seals prone to failure.
Generally, you should inspect and calibrate the sealing temperature at least once a month. However, for high-volume operations or environments with significant temperature fluctuations, weekly checks might be necessary. Always refer to the manufacturer's manual for specific guidelines on calibration frequency and procedures.
Keep the Surrounding Area Clean
Maintaining a clean and organized work area around the carton sealer helps prevent debris from entering the machine and causing malfunctions. Dust, dirt, and packaging materials can accumulate and obstruct the moving parts, leading to jams and potential damage.
Keep the floor and work surfaces near the case sealer free of dust, debris, and packaging materials that could end up drawn into the machine. Additionally, pay special attention to the entry and exit points of the conveyor system, as these areas are prone to accumulating waste that can impede the machinery's smooth operation.
Train Operators
Providing operators with training on proper usage and maintenance procedures is critical for preventing misuse. Well-trained operators are more likely to follow the recommended operating guidelines, reducing the risk of damage caused by improper handling. Regular refresher courses can help keep operators updated on the best practices and any new features or changes to the equipment.
Training for case sealer operators should include the following topics:
- Basic operation: Operators should understand the basic functions and controls of the case sealer.
- Safety protocols: Training should cover all safety procedures to protect operators from potential hazards.
- Maintenance procedures: Operators should learn how to perform routine maintenance, such as cleaning and lubrication.
- Troubleshooting: Training should include common troubleshooting steps to address basic machine issues.
- Proper loading techniques: Operators should know the correct way to load cartons onto the conveyor to avoid jams or misfeeds.
- Adjustments and settings: Training should cover how to adjust settings like belt tension and sealing temperature for optimal performance.
- Emergency shutoff: Operators should understand how to quickly and safely shut off the machine in case of an emergency.
Proper maintenance helps maximize your packaging equipment’s longevity and efficiency. Regular cleaning, inspections, part replacements, and lubrication help prevent wear and tear, reducing the likelihood of downtime and expensive repairs. Keeping the surrounding area clean and providing thorough operator training further contribute to the carton sealer’s performance. Implement these tips to keep your packaging operations running smoothly and cost-effectively.