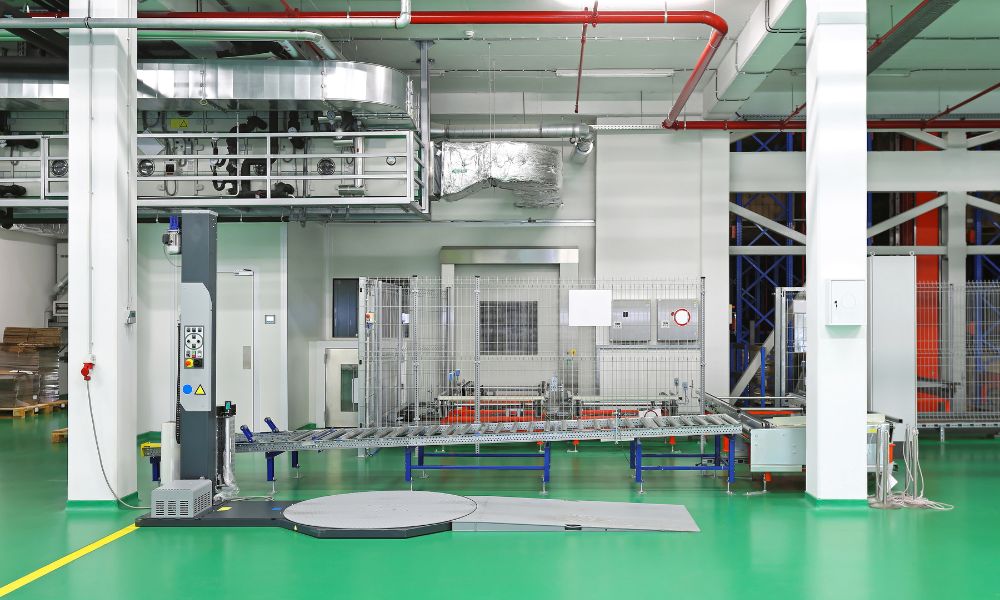
A stretch wrap machine wraps pallet loads with stretch wrap. Optimizing your stretch wrap machine can improve product protection, minimize material waste, and save time in your packaging line and other logistics processes.
You can maximize your equipment’s productivity by selecting the right stretch wrap film, fine-tuning machine settings, and following all necessary maintenance procedures. Discover how to optimize your stretch wrap machine for efficiency.
Understand Automatic vs. Semi-Automatic Capabilities
Choose the best equipment for your business by comparing the capabilities of semi-automatic and automatic machines. Semi-automatic stretch wrappers require an operator to load and unload the machine, adjust settings, and start the wrap cycle. This machine is the ideal choice for businesses with lower output volumes.
In contrast, fully automatic stretch wrap machines take and feed pallets into the wrap zone. The settings on the control system determine how the automatic stretch wrapper processes the load.
Semi-automatic and automatic machines include the following types:
- Stretch wrap turntables
- Robot wrappers
- Rotary arm machines
- Conveyorized stretch wrap machines
- Bundling machines
Turntable wrappers are the most common option. Consider your production volume and load weight and size to find the best equipment for your facility.
Select the Right Stretch Film
Be sure to use the right kind of stretch film for the load type and machine. Consider the load weight and size, as well as stability requirements. High-quality stretch films offer consistent elasticity that contributes to a smoother wrapping process.
Experiment with different stretch film formulations to find the one that maximizes load containment with minimal material. Quality stretch film reduces film breaks and increases load stability.
Cast vs. Blown Stretch Wrap
Cast film and blown film are the two standard types of stretch wrap. Cast film has more clarity, unwinds more quietly, and requires less force to stretch.
Blown films have greater puncture resilience and higher load capacity and can stretch more than cast film. Blown films also have an adhesive that’s sticky to the touch, and the adhesive may rub off on the operator’s hands when touched in warmer environments.
Film Gauge
Gauge is a measurement of the film’s thickness. The higher the gauge number, the thicker and more durable the film. The most common thickness is 80-gauge wrap, which can secure loads up to 2,400 pounds. Keep in mind that there are also high-performance films in the marketplace that are technically lower gauges, but can perform at the level of an 80-gauge film.
Colored Film
Colored stretch film is a convenient way to identify, code, and date product pallets. The film provides the same protection from moisture, dust, and damage as standard colorless stretch wrap.
Understand Load Types
Different types of loads present unique challenges and requirements. Load types are classified as A, B, or C.
A Load Characteristics
Load type A contains uniformly shaped and stable boxes, typically in similar dimensions. The load has uniform vertical and horizontal edges with no protrusions. The A load’s footprint almost exactly matches the pallet deck.
Thanks to load type A’s uniformity, you can often reduce the number of wraps more easily than when wrapping irregular loads. You may also be able to use thinner stretch film depending on the weight and arrangement of the boxes.
B Load Characteristics
B loads include irregularly shaped or sized items that do not stack as neatly as class A loads but still have a somewhat uniform shape. Some edges may catch the stretch film as you wrap.
Irregular loads more often require customized wrapping solutions. You can adjust your machine’s settings to accommodate the load’s shape and dimensions, anchor the load securely, and protect the corners.
C Load Characteristics
Finally, C loads have the highest risk of causing tears and punctures in the film. C loads are often mixed and contain items of different shapes, sizes, and weights, which make the edges uneven.
A uniform load may be classified as a C load if it has a poor weight distribution or is very light or heavy. C loads require careful handling, so proper operator training is crucial for stabilizing each C load. Applying a custom wrap pattern, such as alternating between cable patterns and spirals, can address these unique characteristics.
Adjust the Machine Settings
Another way to optimize your stretch wrap machine for efficiency is to adjust its settings. You can adjust the parameters according to each load’s characteristics and stretch film type. Key settings you should consider include the turntable or arm speed, film carriage speed, and wrap tension.
Thread the Film Correctly
Before turning on the machine, ensure you’ve threaded the stretch wrap as designed. Your machine’s user manual explains how to load the film correctly.
Typically, you will need to guide the film over or around rollers and tension points. If your machine has a pre-stretch mechanism, you’ll need to thread the film through this component so it can stretch the film before applying it to the load.
Adjust the Wrap Speed and Force
Read the owner’s manual to understand how to adjust your machine’s settings. Generally, you can start by modifying the wrap arm or turntable speed. Then, you can set the bottom and top wrap counts.
Next, adjust the speed for spiraling up and down. Finally, adjust the wrap force so the machine applies maximum pressure without breaking the film or twisting and crushing the load.
The containment force is the pressure that holds the load together. The wrap’s tightness and number of layers determine each load’s containment force. The right containment force reduces damage and improves shipping and handling safety.
Follow a Maintenance Schedule
Consistent maintenance will maximize your machine’s longevity and performance. Create a maintenance schedule for cleaning, inspection, and part replacement tasks. Preventive care will help minimize unexpected downtime due to machine breakdowns.
Regularly inspect the machine for worn or damaged components, such as rollers, belts, and sensors. Lubricate moving parts according to the manufacturer’s recommendations to ensure smooth operation and prevent premature wear.
Speak with your equipment supplier to understand which parts they keep on hand and to learn more about maintaining your equipment. The service and repair team will be able to help you attain the correct spare and replacement parts for your machine.
Your Equipment Supplier Can Enhance Your Efficiency
Achieve optimal productivity with your packaging machine supplier’s expert guidance and support. PackSmart is a reputable supplier of high-quality stretch wrap machines, including stretch wrap turntables, rotary arm machines, bundling machines, and more. We also have a reliable service team that can address service needs as they arise or work with you to develop a preventative maintenance plan. Shop with us today for excellent service that will help you find the right device based on your production volume, load types, and business goals.
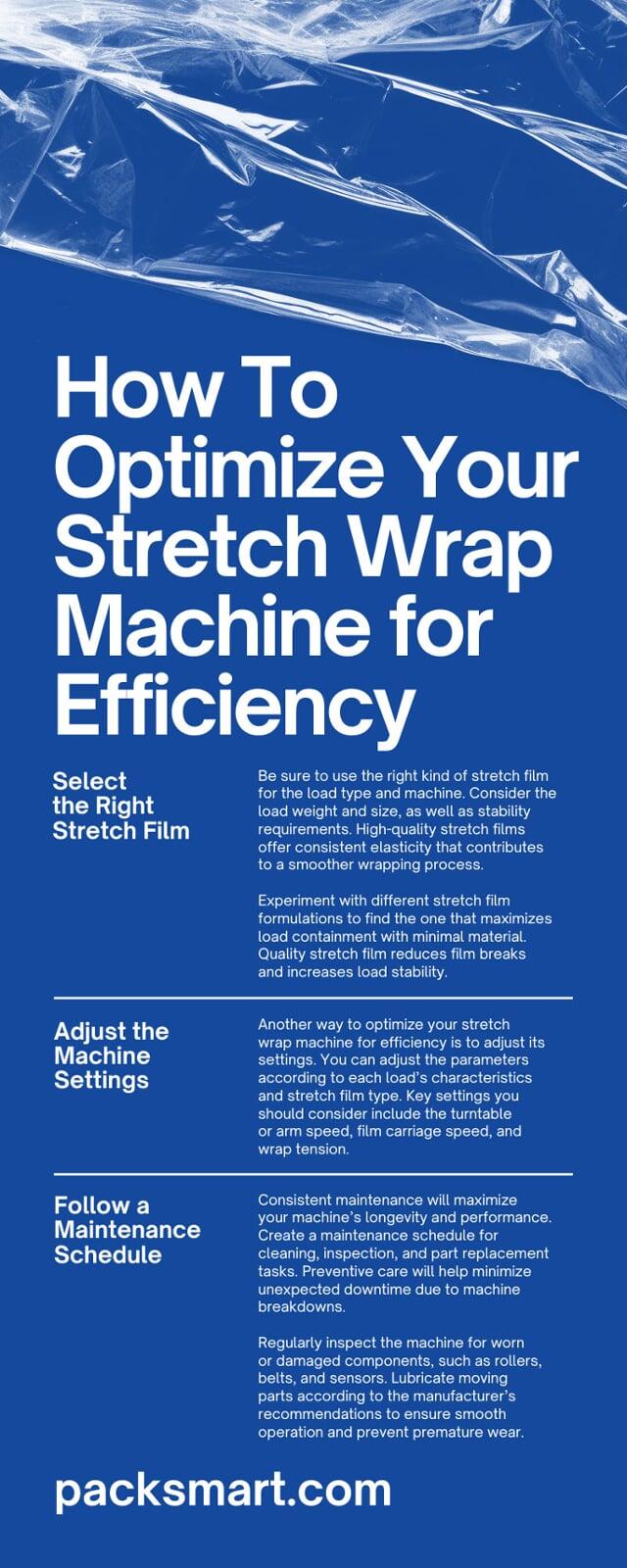