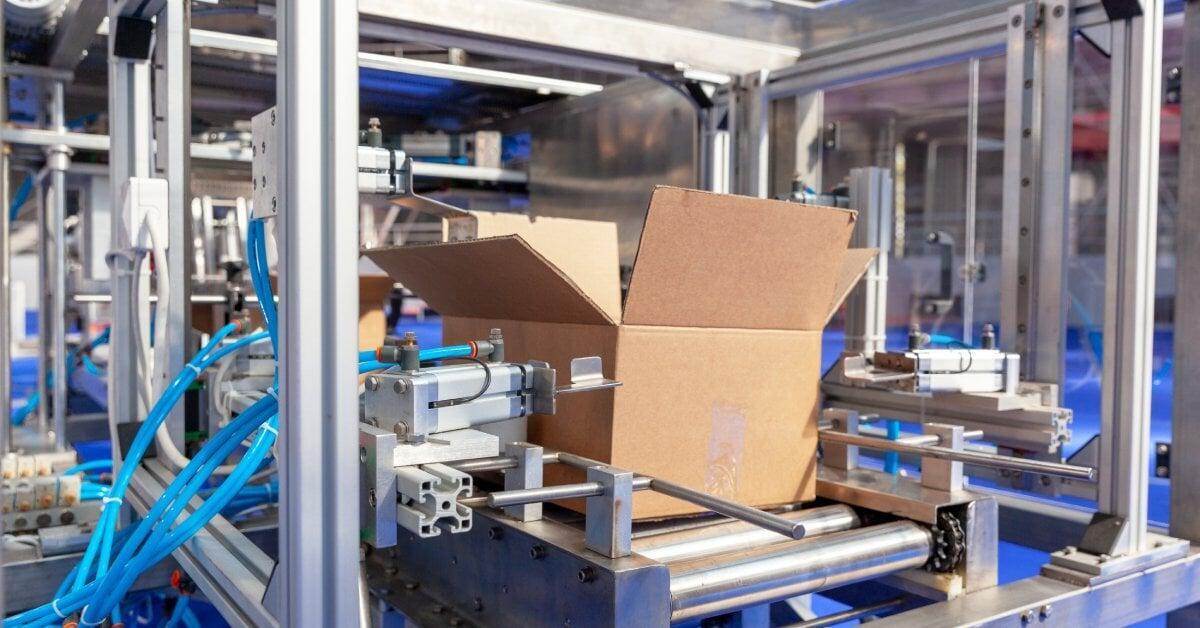
Case erectors—essential machinery in many industries—play a vital role in automating the packaging process. Designed to fold and seal cardboard boxes quickly and efficiently, they streamline operations, reduce manual labor, and increase productivity. However, even the best equipment can falter without proper upkeep. That’s where maintenance comes in. Regular maintenance extends the lifespan of your case erector and ensures that your production line runs smoothly, minimizing unexpected downtime.
This guide will explore why case erector maintenance is a must for maximizing uptime, as well as outline common issues users may encounter and how to troubleshoot them.
Understanding Common Issues With Case Erectors
Before exploring the importance of maintenance, it’s helpful to identify the typical challenges faced by case erector operators. These challenges often come down to wear and tear, improper handling, and environmental factors.
Frequent issues include machine jamming, which can arise from misaligned parts or poorly adjusted guides. Jamming often brings production lines to an abrupt halt, delaying operations and wasting time trying to resolve the issue. Additionally, worn belts and rollers may lead to uneven movement of cases, resulting in improperly folded or sealed boxes. It is also common to encounter problems with adhesive application, such as inconsistent glue or tape dispensing, which can undermine the integrity of boxes.
Material quality also contributes to common case erector issues. Low-quality cardboard deteriorates faster and may cause faulty feeds, while inadequate tape or adhesive can result in poorly assembled boxes. Environmental factors, such as dust accumulation and humidity, further exacerbate these problems by impacting the machine’s components. Addressing such challenges starts with a disciplined maintenance approach.
Crafting a Comprehensive Maintenance Schedule
Regular maintenance is integral to effective machinery management. By adhering to a systematic schedule, operators can anticipate and mitigate potential issues before they escalate. For case erectors, you can divide maintenance tasks into daily, weekly, and monthly routines.
Daily Maintenance
Daily maintenance involves visual inspections to check for any obvious signs of wear or damage. Operators should confirm that belts, rollers, and seals are in good condition, ensuring that no parts are misaligned or obstructed by foreign objects. Clearing away debris and cleaning moving components prevents dust buildup, which could impair machine performance during operations.
Weekly Maintenance
Weekly maintenance requires more in-depth attention. At this stage, lubrication of moving parts is essential. Neglecting lubrication leads to increased friction between components, causing premature wear and reduced efficiency. Operators should also test sensor functionality to confirm that the machine can detect and process cases reliably. By verifying alignment and adjusting guides, operators further ensure that boxes are fed, erected, and sealed correctly.
Monthly Maintenance
Monthly maintenance involves comprehensive inspections and updates. This includes tightening loose bolts, examining motor performance, and inspecting electrical connections for signs of corrosion or wear. Operators should replace parts such as belts, rollers, or adhesives before they become fully worn out, preventing disruption during operations. A monthly performance test verifies that the machine operates as expected under normal production conditions.
By sticking to a structured routine, your business can keep the case erector in peak condition, eliminating the need for costly repairs and improving overall equipment effectiveness.
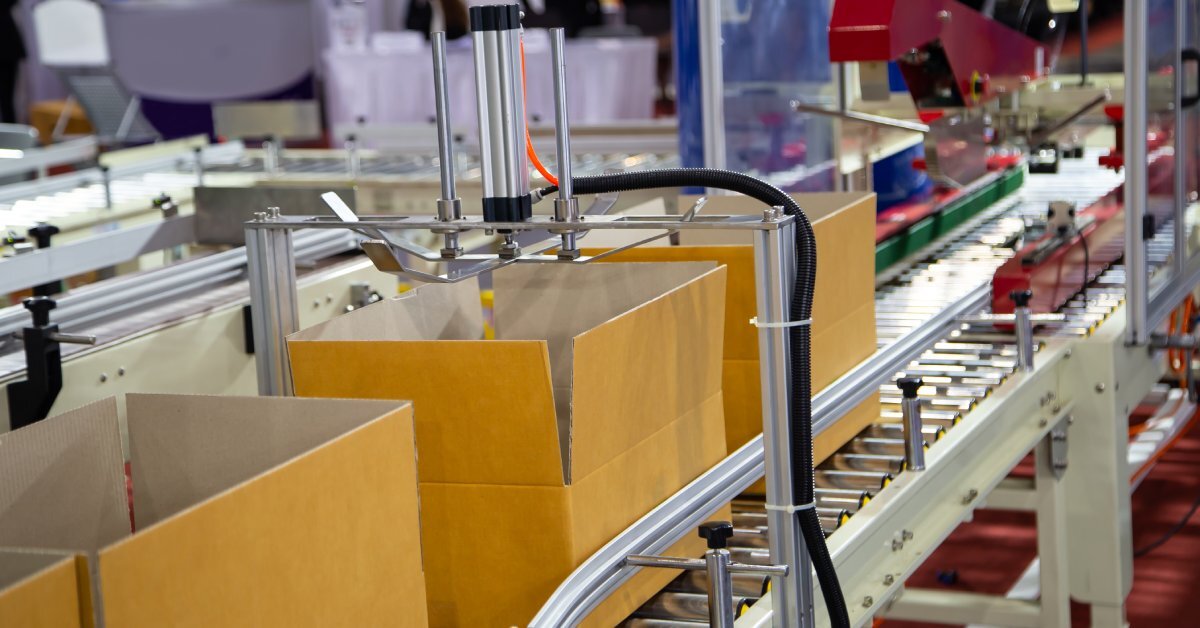
Troubleshooting Tips for Common Problems
Even with meticulous maintenance, the occasional issue may arise. Knowing how to troubleshoot effectively can significantly reduce downtime and restore operations quickly.
Jamming or Box Feed Difficulties
When faced with jamming, it’s important to check for blockages in the machine’s path. Clearing stuck cardboard or adjusting misaligned guides often resolves this issue. For box feed difficulties, users should verify the quality of the cardboard and adjust the machine settings to compensate for varying material thicknesses.
Adhesive Problems
Adhesive problems are another common challenge. Adequately filling glue tanks and properly applying adhesives typically rectifies irregular application. It’s equally important to confirm that glue or tape dispensers remain free of residue, which can block flow and reduce adhesive efficiency.
Vibration or Unusual Noise
For cases of vibration or unusual noise, inspecting the machine’s bearings, bolts, and moving components can help identify potential issues. Vibrations often stem from loose parts or unbalanced mechanisms, which you should tighten or adjust to restore stability.
Faulty Programming or Outdated Settings
Operators should periodically reset the machine’s software or calibrate its sensors if detection errors arise. Sometimes, faulty programming or outdated settings may cause the machine to misinterpret alignment or box dimensions. Addressing these issues ensures smooth, uninterrupted performance.
Implementing these quick fixes minimizes downtime and gets operations back on track. For ongoing problems, however, consult the machine’s technical support team or refer to the service manual.
Recognizing Why Consistent Maintenance Is Non-Negotiable
The benefits of consistent maintenance extend far beyond resolving immediate concerns. Regular maintenance contributes significantly to maximizing uptime, reducing operational costs, and improving final product quality.
Maximizing Uptime
Uptime, a critical metric for manufacturing and packaging lines, refers to the percentage of time a machine operates without interruptions. Case erector maintenance is a must for maximizing uptime and maintaining reliability, reducing the frequency of unplanned shutdowns. By avoiding production delays, businesses can achieve higher throughput, meet deadlines, and keep customers satisfied.
Financial Savings
Financially, maintenance is a cost-effective alternative to unplanned repairs or complete equipment replacement. With routine checks to prevent wear and tear from spiraling into mechanical failure, businesses save on repair costs and avoid revenue loss from halted production.
Product Consistency and Quality
Another key advantage of maintenance is its impact on product consistency and quality. Properly functioning case erectors produce neatly assembled, durable boxes that meet customer expectations. Poorly maintained machines, on the other hand, may produce subpar results, potentially damaging a brand’s reputation and customer relationships.
Sustainability Goals
Regular maintenance aligns with sustainability goals by extending the life cycle of case erectors. By minimizing waste and reducing energy consumption, businesses responsibly manage their resources, reinforcing their commitment to environmentally friendly practices.
These cumulative benefits highlight why maintenance should be an integral part of any operation that relies on case erectors.
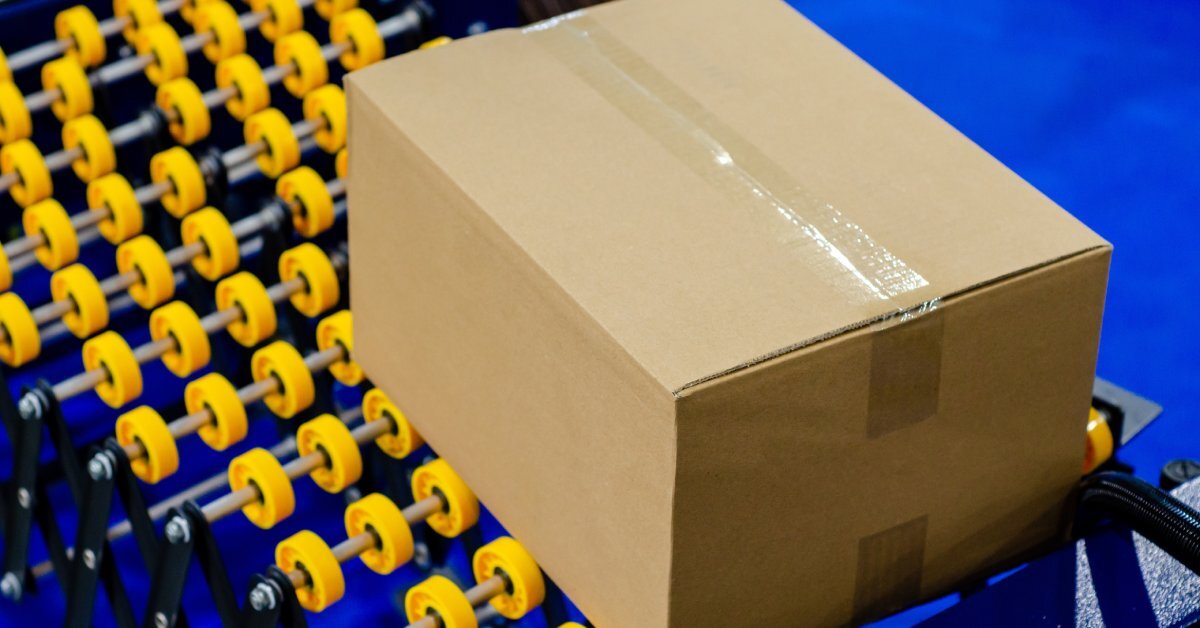
Maximizing Your Case Erector’s Longevity
Every production line strives to deliver efficiency, reliability, and top-tier product quality. Case erectors are a vital component of this vision, automating the labor-intensive task of box assembly to meet the demands of modern packaging.
However, as machinery works tirelessly to power your operations, it’s important to protect this investment through consistent maintenance. From daily visual inspections to monthly performance tests, creating and adhering to a structured upkeep schedule is critical. This prevents unexpected breakdowns and offers long-term benefits in the form of reduced costs, improved uptime, and enhanced product quality.
If you’re in the market for a high-quality, reliable case erector for your business, check out PackSmart’s automatic and semi-automatic options. You can easily integrate our case erectors into any setting. Contact us today to learn how our customizable equipment can improve your packaging process and increase production efficiency.